A bold vision for a climate-neutral and competitive Europe
Next event In person & livestreamed
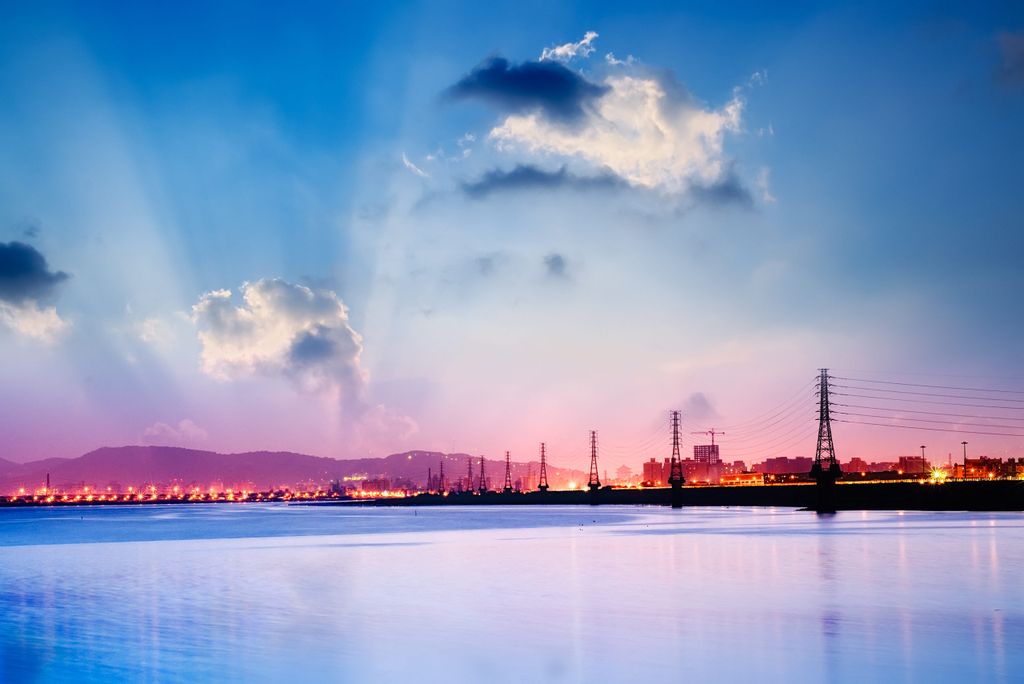
- Area of Expertise
- Climate, Energy & Natural Resources
Climate, Energy & Natural Resources
Senior Manager Construction Advocacy and Sustainability - EU Government Relations BASF Group
Smarter construction offers the greatest opportunity to deliver cost-effective cuts in the greenhouse gas emissions that cause climate change. Buildings account for 40% of global energy consumption and are responsible for a third of the planet’s carbon dioxide (CO2) emissions. So business, academia and science are together designing new urban landscapes, where cities are living and interconnected, solar energy is produced in every façade, and smart insulation regulates the internal environment.
Yet for the most part, we live in houses built decades ago, which waste energy and cause the emission of large quantities of CO2. The biggest contribution to a reduction in CO2 emissions from buildings will therefore come from renovating the existing building stock.
The Brunck residential quarter, just outside the gates of BASF in Ludwigshafen, is a striking example of how to cut energy consumption and CO2 emissions by renovating existing buildings. For the most part, the district’s 500 dwellings are blocks housing multiple flats dating back to the 1950s. In the mid-1990s, the floor plans of these apartments no longer met modern needs. BASF’s housing company, the city of Ludwigshafen and the state of Rhineland-Palatinate drew up a comprehensive modernisation programme, which has reduced the amount of heating fuel needed by 80%. It consisted of projects targeted at different levels of performance. Starting from an average heating energy consumption of 21 litres of heating oil per square metre (210 kilowatt hours per square metre per year, or kWh/m²year), renovations reduced the energy consumption to 7 litres (70 kWh/m²year), 5 litres (50kWh/m²year) and 3 litres (30kWh/m²year). For the most part, the buildings were modernised in line with the low-energy house standard, and new construction was carried out following the passive house standard (1 litre – 10 kWh/m²year).
The modernisation of an older building to meet the 3-litre energy consumption target has attracted attention and acclaim well beyond Ludwigshafen. Its success is based on a cutting-edge energy strategy using innovative construction materials. The building’s maximum consumption of only around 3 litres of heating oil per square meter per year puts its energy requirements between one-seventh and one-tenth of non-modernised older buildings. For an apartment measuring 100 square metres, heating costs have dropped from around €1,400 to €200 a year.
The addition of graphite improves the insulation performance by up to 20%
The building was insulated with panels at least 20 centimetres thick made of Neopor®, which has considerably better thermal insulation properties than conventional materials. Like its ancestor Styropor®, the foam plastic invented by BASF in 1950, Neopor is composed of small beads of polystyrene. However, the beads in Neopor contain tiny graphite particles that reflect thermal radiation and give the material a silver-grey hue. The addition of graphite improves the insulation performance by up to 20%.
The Passive House Institute also strongly recommends avoiding thermal bridges in the building’s envelope (gap or discontinuity in the insulation layer) that make it easy for heat to escape. To prevent heat from escaping via the balconies, for example, shunts were replaced by a structure not directly attached to the building.
The fresh air supply for all rooms in the building comes from a controlled ventilation system, which sucks used air out of the kitchen and bathroom and passes it through a heat exchanger. The exchanger transfers up to 85% of the heat from the used air to fresh air, which then flows at a pleasant temperature into the living room and bedrooms. It also filters out contaminants.
The windows in the 3-liter house are triple-glazed, and their synthetic frames feature a core of polyurethane insulating material. Inert gas between the panes provides additional protection against the cold. A single-glazed window allows around seven times as much heat to escape. The windows were enlarged to let more light enter.
These technologies have become standard practice, and BASF continues to innovate. The performance of Neopor® insulation has been further enhanced and new innovative materials, such as Slentite®, have been developed. This is a polyurethane-based aerogel insulation panel with very high insulation performance, making it suitable when there is limited space available for insulation.
Each renovation project is different, but the aim is always to make it win-win
The Brunck district modernisation has also accommodated new residential requirements identified through workshops held with tenants. Floor plans incorporated the identified requirements, an optimised parking scheme was implemented, and green areas were created, as well as areas for recreation and relaxation.
Ten years after the renovation, the economic, ecological and socio-cultural results were assessed in a long-term study. This showed that energy efficiency measures are durable and equally beneficial to tenants and landlords. Besides cost savings, tenants appreciate better comfort and are positive about the renovation. More importantly, between 2000 and 2015 the BASF housing company thermally renovated around 3,500 housing units, representing 40% of its housing stock. This corresponds to an annual renovation rate of 2.6%, far above the EU average of 1%.
Each renovation project is different, but the aim is always to make it win-win. For the tenants, rent increases after renovation have to be lower than the energy cost savings. They also benefit from increased comfort and quality of living space. For the housing company, the investment has to be economically viable in terms of increased revenue and asset value. Even with these conditions, primary energy consumption is reduced by about 70% to 80% in most cases.
The current renovation rate in Europe is insufficient to meet the EU’s energy and climate targets. To meet the ambitions of the Paris Agreement, the EU building stock needs to be renovated to an energy level of nearly zero by 2050. The European Commission’s November 2016 Clean Energy Package supports the energy transition, and the key role of buildings was highlighted in the Energy Performance of Buildings Directive. But no clear building renovation targets have been set. The Brunck district renovation has demonstrated the feasibility of cutting-edge energy savings in existing building stock, so it is now up to governments to take the necessary steps to increase the renovation rate and depth.
This article is from Friends of Europe’s discussion paper ‘Cities – the new policy shapers in the energy transition’, in which international experts, policy-makers and entrepreneurs report from cities and regions all around the globe acknowledging cities’ evolving and prominent role within the energy transition. Cities are teaming up, creating coalitions and sharing knowledge on the most advanced and innovative solutions to tackle climate-related risks.
Next event In person & livestreamed
Past event In person & livestreamed
Past event In person & livestreamed
Past event In person & Livestreamed
Stay informed
We use cookies and similar technologies to adjust your preferences, analyze traffic and measure the effectiveness of our campaigns. Learn more about our privacy policy.